James Carter is a 2025 Nuffield Scholar and the Assistant Production Manager at Australian Agricultural Company (AACo).
In this instalment of our series ‘Meat the Supplier’, we sat down with James to discuss his research on using technology to drive profitability and sustainability in the beef industry by improving carcase yields.
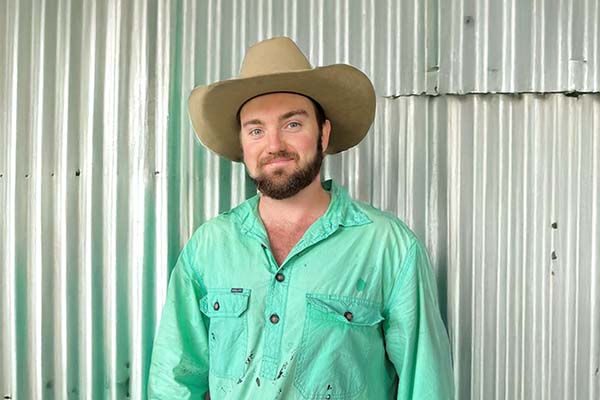
What is your background, and how did you become involved in and passionate about agriculture?
I grew up on a cattle property in southern NSW near Crookwell, and I am the seventh generation to grow up there. Our family has the oldest registered fire brand in Australia, and I have been fortunate to have learnt from my grandfather, John Carter, as well as my father, Ben and mother Cath.
At the property, we have implemented an artificial insemination (AI) program where we've started introducing French Normande straws into our herd, crossing with Charolais over the years and my grandfather has experimented with around 17 different breeds to find the best cross for our production. We've eventually come to this hybrid animal between a Normande and a Charolais that has improved our overall productivity and performance.
I moved up to Brisbane to finish school, and did a carpentry apprenticeship, but at the tail end of that I started finding my way back into agriculture where I realised that was where my true passion was. I started working at a company called EC Rural, which ranged from international sales to being on the ground at the Casino abattoir.
I then reached out to a contact at Australian Agricultural Company (AACo) to see if I could gain some more experience in an abattoir setting. When I was at the farm, we would just put the cattle on the truck and didn't really know exactly what happened to them after that. So I was keen to gain some experience in a processor. What started as a bit of work experience turned into getting a job with AACo, where I really started learning the fundamentals of processing; from revenue maximisation, performance metrics, costings, food safety, and quality assurance, just to name a few things. One of the more important roles being a third-party processor is maintaining a strategic and collaborative relationship with those third parties, as we do not own the abattoir.
After two years working in that role, I was promoted to Assistant Production Manager, where I help manage a team and the two service kills, and also work alongside sales and shipping on documentation, making sure products are within specification, and liaising with the feedlots with cattle coming from the feedlots to the abattoirs.
I think the really cool thing about my role is that I work fundamentally for AACo, but I also have an interest with JBS Beef City and Australian Country Choice. Being mentored and working with them in a very collaborative way has been really beneficial for me and it's giving me a great foundation in my learnings as I hopefully become a subject matter expert in processing.
Every day I learn more and more, so I don't think I'll ever become a full subject matter expert, but it's a great part of the supply chain to be in.
What made you want to apply to become a Nuffield Scholar?
I heard about Nuffield a couple of years ago. Munro Hardy came to talk at an Intercollegiate Meat Judging (ICMJ) conference, and it blew my mind that there was an opportunity like this out there.
For me personally, Nuffield is a way to help the industry for the better. It is a program that gives me the ability to grow global networks, and also to put time and money into this project and into my personal development. Another really cool part is the opportunity to learn from people of different backgrounds and also other industries. Nuffield is not just about beef; it's about every single part of the agricultural supply chain. Being able to learn from what other industries do and maybe bring those learnings back to the beef industry as well.
Tell us a bit more about your chosen study topic, and how it may impact both producers and the wider sector.
My topic is using technology to drive profitability and sustainability with the improvement of carcase yields. As an industry, there is huge potential to start breeding higher performing carcases if we have the technology to measure them. The way we look at yield is so average driven currently. For example, if we process 1000 head, we take an average carcase weight of those 1000 head, then take an average piece weight of, say, 2000 pieces that come off those head, and that's our output. There are so many variables which aren’t being captured.
When we put it in perspective of studies that have been done on the beef industry, there is anywhere between 20 per cent variance from the top and bottom performers in a carcase. If you put that in the context of a heavy grain-fed animal, you might get 300kg of saleable red meat from a live animal which was 700kg, and around 60kg variance from the top and bottom.
Then, the average standard deviation from carcase to carcase is around 6 per cent. That might be 18kg. If you're selling high-quality product that can be around an average sale price of maybe $20 to $30 per kg, depending on what you're selling, that is a lot of money we are potentially missing out on from these low performing animals.
If we can start breeding these animals out of a herd using technology to standardise what a good yielding carcase looks like, it will be game changing.
Processors pay premiums for grids on marbling or MSA scores, and I foresee this would become an attachment to the grid, similar to what Gundagai Meat Processors have done with their lamb, paying a premium for higher yielding animals.
I want the key outcomes for this project to drive collaboration between processors and producers, because I want each part of the supply chain to pick up a premium. One does not work without the other. On the producer side, to implement this, a key part will be having forums and helping producers understand and process what's going on. If they put their cattle on a truck and then get paid a premium for one carcase over another, they are going to be asking why which is why it must be articulated clearly.
And so, the reason that processors would pay a premium for a higher-yielding carcases is for the sustainability and profitability benefits. When we are looking at emissions intensity, it is based on saleable red meat and kg per head. Under this new model, we would be reducing our emissions intensity because we're getting more saleable red meat from each body with less waste. We are also reducing processing costs because we are seeing just as many animals go through the processor at the same pace, but getting more red meat from each carcase. Eventually, we would also see efficiency improvements and quicker throughputs because we are not having to trim carcases up quite as much.
I hope this would then be the catalyst for the industry to implement artificial intelligence as we improve that consistency, and from there we could start using a lot more robotics, and eventually that may improve the labour crisis we're seeing across the industry. Australian labour is amongst the most expensive in the world, so we need to find ways to fight those inflationary costs.
The other thing with this technology is that once the device is calibrated, we have the potential to marry it up with devices like MEQ live scanners, to understand when animals are properly finished. Particularly for grain-fed cattle, we could work out when that muscle conformity is fully optimised.
We’d also be able to segregate carcases based on the best markets they are suited for. Being able to get that consistency is just another benefit.
How do you plan to study the topic throughout the next year?
At the moment I'm in discovery mode, so meeting with key contacts at Meat & Livestock Australia, CSIRO, Murdoch University, University of New England, AACo’s processing partners and building that database of the right questions to ask when I go and meet with contacts overseas.
At the end of the day, I want to make sure that this report is actually used, and that I'm doing everything I can to get the most out of this opportunity over the next two years. There have been studies done on this already, but I want to be able to piece all of that good work together to then push this amazing topic even further into implementation.
As far as travel goes, we start off in March with a visit to Canberra, and then I will head to New Zealand, meet all the other global scholars, to get to know our cohort before we start doing group travel. We are still deciding on the dates for the group travel and but the trip I would like to attend is in May-June, and would take me to Singapore, Taiwan, Romania, Poland, Zimbabwe and Chile. The group travel is all planned by Nuffield which means we’ll be learning about multiple different industries and supply chains, not just beef.
I would also like to do some individual travel at the end of that, and go to the United States. I’d like to look at a few different plants, like JBS USA, because I know they've started looking at some objective yield technology over there.
After the US, I would like to go over to Europe, mainly Denmark, Germany, the Netherlands, and Ireland, which is where most of this technology is either being implemented or designed.
Back to your role at AACo now. With the different types of breeds that AACo run, what kind of cattle do you find produce the best results across yield and meat standards?
From a breeding perspective, we are always trying to improve incrementally.
We have a big focus on our Poll Wagyu at the moment for animal welfare reasons, to prevent bruising and dehorning. We always want to do the right thing by the animals, and it also has a profitability impact at the end of the day.
As for yield, as I said earlier, there is no real way to work out which breed yields well. Particularly when you have such a different genetic makeup with multiple breeds that go through abattoirs and everything is so average driven, it's very hard to understand which individual carcases yield better than others.
There are trials which have been done where you physically de-bone a carcase, one at a time. It takes a few hours to do so because you need to weigh every single piece and trace it back to that carcase. However, commercially that is not a possibility. So that is why this technology I am studying will be such a gamechanger into the future. To be able to say ‘that animal came from this sire’ or ‘this mother is breeding this high yielding carcase because of this phenotype’, and then we can start using those embryos and phenotypes and start spreading that across a herd.
So, we don’t have the technology right now to say that a certain breed breeds better than another, but I suppose that is what I am hoping to fix!
What portion of production at AACo is grass-fed versus grain-fed?
Anything that goes into our branded beef supply chain, that goes through the feedlots is grain-fed. However, our Wagyu animals that are finished on grain still spend the majority of their lives roaming large paddocks eating grass on big properties in Queensland and the Northern Territory. We do have a smaller grassfed program as well.
Cattle in the north will go through live export pathways, and then the rest of the herd, the composite animals, will go to lives sales or OTHs. So that area is all grass-fed until they are purchased, and the next steps are determined by the buyer.
How much has the herd shifted towards Wagyu over the last 10 years?
I’m unsure on the numbers noting that we acquired the Westholme herd in 2006 and Wagyu has been one of our primary focuses ever since. We now sell our Wagyu under three primary brands – Westholme, Darling Downs and 1824. We recently reintroduced 1824, which celebrates our 200 years of history.
With the improvement in Wagyu genetics, how have marble score results improved?
We are always aiming for constant improvement, and that drive for progress is partly behind my project to improve carcase yields
One focus area has been analysing and maintaining marble score with the Poll Wagyu push. That's been a really big push genetically as I said earlier; we are reducing any dehorning for animal welfare reasons, and for the safety of our employees. It also means we can prevent them from puncturing each other with their horns so don't have bruising and then loss of product when it gets to the processor.
We see basically the same meat and marble quality from the Poll animals, the main difference is that lack of bruising and or injuries.
Do you have any interesting facts about the supply chain or industry which producers may not know?
I think the conversion from a live animal to saleable red meat is an interesting one.
So, based on a heavy grain-fed animal, we might start with a live weight of 700kg. When that animal goes into the processor, 42 per cent comes off on the kill floor.
A side note, everything is used, it’s a very sustainable process, and nothing goes to waste whatsoever.
Once we undress the carcase and we get it to meat and bone, we get a hot standard carcase weight of around 406kg. So, we've started with a 700kg live animal to a 406kg hot standard carcase weight. That will be chilled, and then once everything is boned out, on average you're left with about 300kg of saleable red meat. From that 300kg, 200kg will be primal and the other 100kg will be trim on average.
So, for the producers, when you're in your paddock next time and you see 100 head of cattle running around, the red meat volume of 33 head will go to trim on average depending on cut plans.
That is why it's such a big focus of the industry to look at maximising carcase yield.
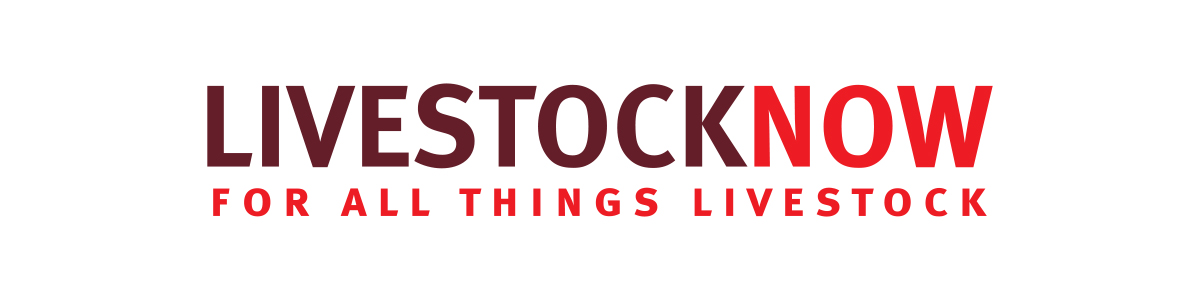